I didn’t think I would have this done by today but in a burst of fevered work, I finished up the light cruiser model so that’s what I’m writing about today. The image to the right shows the final model (click for the full-sized image). Let’s talk a bit about the ship.
First off, I’ve been calling this the light cruiser but on the Federation Ships boxed set of miniatures that the original came in, it is labeled as a Destroyer. However, it’s much too big to be a destroyer so I’ve always considered it a light cruiser, although it could arguably be a heavy cruiser also.
The frigate model is 2.25 inches long. Based on the size given for the frigate in the rules, this makes the model 1/2500th scale. The destroyer is only 30% longer and so at that scale should be about 2.9 inches long. This model is 3.75″ long. As a light cruiser it is a 1/3800th scale model which makes a little more sense to me. The battleship model is at 1/5900th scale so that would put it in between the scales of the frigate and the battleship and similar to the sathar light cruiser model which is at 1/3500th scale.
Here’s a picture of the two original miniatures side by side. They are roughly the same size (when I’m comparing them and quoting scales, I’m looking only at the fuselages and not counting the engines) and have basically the same volumes. So you’d expect the ships to be of similar sizes as well. So that’s why I’ve been calling this the light cruiser and not the destroyer despite what the box says.
With that out of the way, let’s look at creating the model.
The Fuselage
The first step was to build the basic fuselage that all the other bits would be attached to. This was fairly straight forward as it was mostly just some cylinders and cones hooked together. The calipers provided the lengths and diameters and that got us from the stern up to the neck just before the bow.
This is where I made my first deviation from the original miniature. On the mini, the bow is a hexagon from back to front so it extends out beyond the neck portion of the ship just a little on the sides. I decided to make if flush there and so used the software to smoothly transition from the circular neck to the hexagon, just like I had done on the frigate model.
At this point, I also added all the ridged trim to the edges of the model. I ended up making my trim a little more finely grooved than in the original miniatures. With that done, I had the basic fuselage and could start adding details.
The Engines
As you can see from the photo above, the engine structure on the UPF ship is much more complicated than the sathar one. That was part of the reason I started with the sathar ships several years ago when I first started making the reproduction models – it was simpler. However, I knew I was going to have to tackle this.
Then I got looking at the engines for the battleship model as well (they are not attached to the model like they are for the light cruiser). On closer inspection, I realized that they were exactly the same! Which meant that once I created a model of the engine, I could use it for the battleship as well.
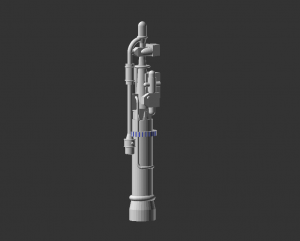
So I busted out my calipers and started measuring. I quickly realized that that wasn’t going to work too well as there were little bits and pieces that I couldn’t reach with my calipers to make measurements. So I also took a series of images of the engines from each side that I could pull up in a graphics program and measure the number of pixels across a given feature was and convert that to millimeters to use in making the model. The result was the model to the right.
If you look closely, it’s a little bit cleaner than that one on the model. That’s because I’ll be 3D printing these and don’t have to pour molten lead into a mold. That allows me to leave of features that on the miniature look like they are there just to get the lead to flow into all the right parts. So it’s not an exact replica, but rather a close match.
The Guns
The next bit was to do the gun turrets. They are all the same and not quite equally spaced around the body. This was another instance of being able to make a single model and reuse it. It was also at this point that I discovered that there are two slightly different versions of the light cruiser miniatures.
Over the years I have acquired four different Federation Ships boxed sets, primarily in an attempt to get one that didn’t suffer from lead rot. It seems that these ships were particularly succeptable to that, primarily the battleship model. I finally ended up with two good sets, one of which had a coat of primer applied. In looking at the light cruiser models from these two sets, I noticed that the gun turrets were different between the two. On of the minis (the painted one) had more details on the turret than the other. I pulled out my other two cruiser minis to check and there was one of each in that pair as well. The difference is minor but I chose to model the more detailed version.
Again, like the engine, there were some features, mainly material supporting the gun turrets, that were there to help the lead flow into the mold that I left off in my model.
Details, Details, Details
With the easy and repeatable parts out of the way, it was time to start adding in the individual details all along the surface of the ship. I simply started at the stern of the ship and worked my way forward using calipers, rulers, and my good, old-fashioned Mark I eyeball (assisted by a magnifying glass) to determine the size and position of each of the features on the model.
The boxes, cylinders, and spheres were easy enough to add in as those are native shapes the modeling software I use produces. The really tricky part was all the piping along the body of the ship. Getting those shapes created and positions was a bit trick but by the time I got to the bow of the ship I was getting pretty good at the process and had built up some tools that simplified it that will help me in models going forward.
And then it was done. I wasn’t keeping exact track of the time but I think I spent something on the order of 10-20 hours producing the model. Now it was time to print.
Printing
If you remember from my review of the AnyCubic Photon printer, the print time is directly related to the height of the object printed. Since this model was small enough that it could lay flat on my print bed, I had two choices, flat or vertical. I was going to print this with the grey, opaque resin because I wanted to get more familiar with that resin and because it makes the details a little easier to see. The opaque resin takes longer to print and cure as you have to spend a little more time on each layer when printing (16 instead of 10 seconds). So printing flat meant a 3 and a quarter hour print while a vertical print meant a 12 hour print. In the interest of testing, I went with the shorter print (I really wanted to see a print that day and not wait all night).
Once the print was done and cured, I started looking it over to see how it compared to the original miniature. The “down” side looked fine, there were some variations but overall it looked fine. Then I turned it over. The “up” side did not look nearly as good and felt almost melted to me. I realized that this was from resin pooling on the upper surfaces and not draining off and then slowly curing during the printing process. I also noticed some warping due to not having enough supports in certain places. It looked like a flat print was not going to work. So I set one up to print overnight in the vertical orientation.
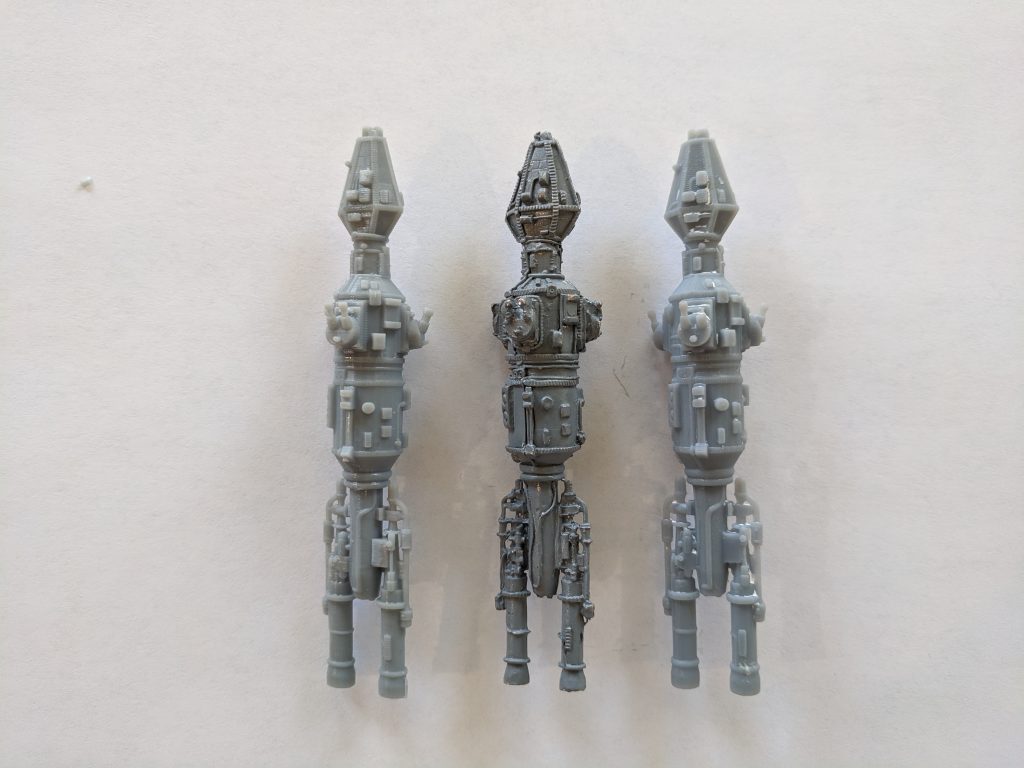
This first image shows the three minis side by side. The original metal miniature is in the middle (this is the primed one). On the left is the vertically printed mini and on the right is the horizontally printed one. This is the “down” side of the horizontally printed mini. Comparing the two printed minis, they look about the same on this side. Although I think the vertically printed one is just a little crisper.
Comparing the plastic and metal minis, I realized that despite always reducing the size of the features as I measured them off the unpainted mini, a lot of the features came out slightly larger. Also, the metal miniature still wins on the details in some places. I think I could fix that but I’m happy with the way it looks.
Turning the model over we get this view.
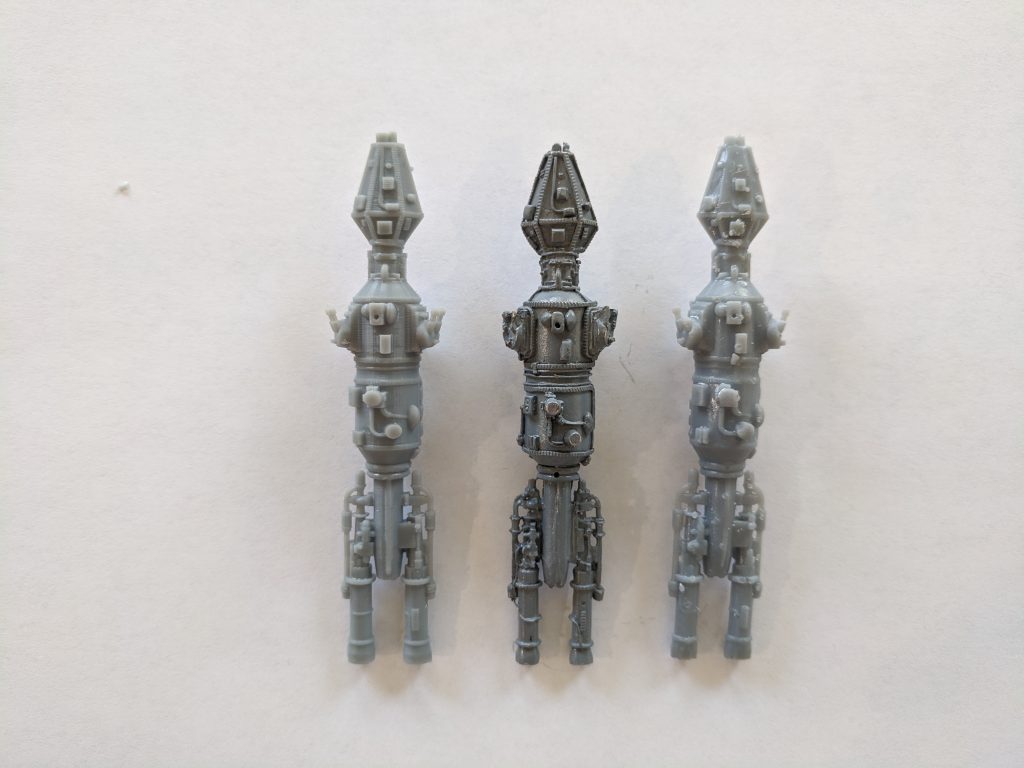
Here you can immediately see the issue with the printing on the horizontally printed model (on the right). The features are just not as crisp and clean. As I said before, to me it looked a bit melted. You can’t really see it in these images but the bow and ends of the engines are pinched and skinnier than the other model and the original. This is due to flexure in the printing process that could probably be fixed with more supports (I don’t think there were supports on the very tips because they were higher up and therefore didn’t technically need them). However, the issues with the remainder of the surface make this not really worth pursuing. This model will need to be printed vertically for best results.
Here’s another picture of the first side with the models in a slightly different orientation that includes a ruler for scale.
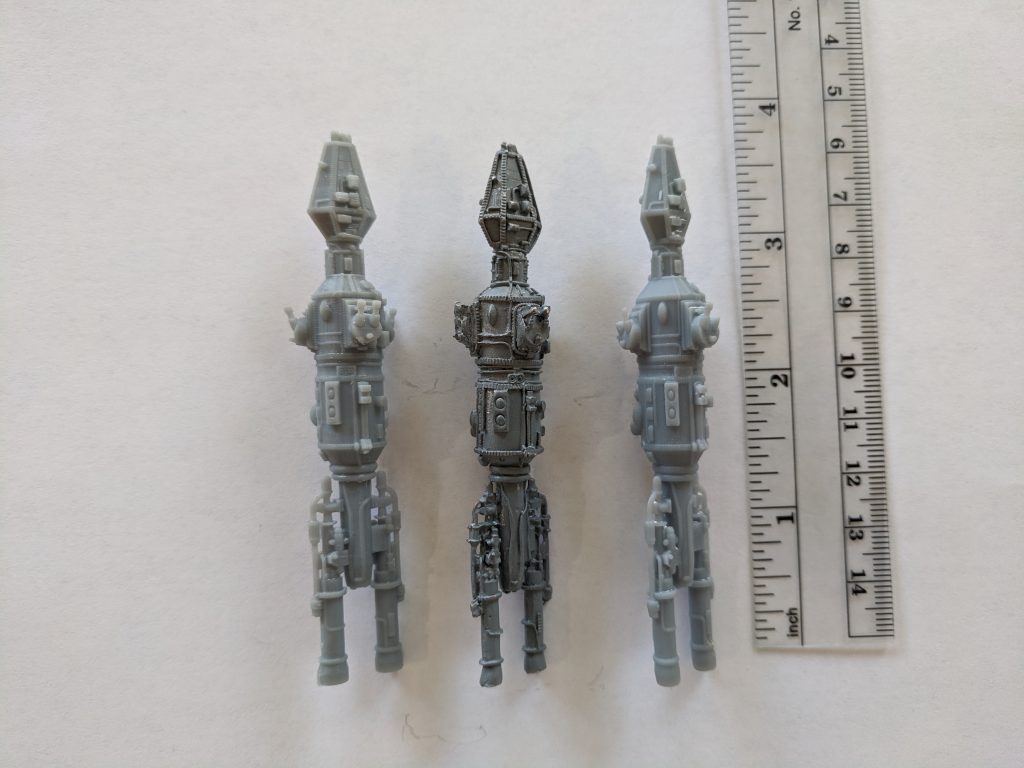
In this view, you can actually see a bit of the curvature I was talking about in the bow and engines of the model on the right.
Wondering if the opaque resin was part of the problem of the parts looking bigger or less distinct (due to the longer curing time while printing) I printed another vertically-oriented one win the translucent green resin that I did a lot of the other ships in. I don’t have a picture but I decided that there really wasn’t any difference between the two other than it was harder to see the details on the green one.
Final Thoughts
This model is good to go. I could tweak it in the future to make it look a little bit more like the original miniature but I’m happy with it the way it is so if I do tweak it, it will be some time in the future when I’ve got the rest of the line of ships complete.
I’ll be sending the model file out to my Patreon supporters later today. I’ve added this model to the price list on the Order Miniatures page for those that want to order minis for their collection. It’s priced just like the Sathar light cruiser at $2.75.
Some time in the next month (probably after we get issue 26 of the Frontier Explorer out the door), I’m going to start posting the model files up on DriveThruRPG for download as well. The models that are reproductions will be offered as pay-what-you-want while the ones that are original to me will have a small cost.
Next up is the UPF battleship. I already have the gun turrets (but not the bases, those are different) and the engines ready to go. There are a lot of repeated features on that model so it might go faster but it will definitely be November before it’s done. After that, I plan on filling in the gaps in the ship lines by designing a UPF destroyer, minelayer, and heavy cruiser, and then the assault carriers for the UPF and sathar. That will give all the ships necessary for full fleet engagements. After that I’m going to go back and tackle the pirate frigate, freighter, and privateer minis from the original sets to complete all the reproductions. There might be some new ships thrown in along the way as well.
Feel free to share your thoughts and comments below.